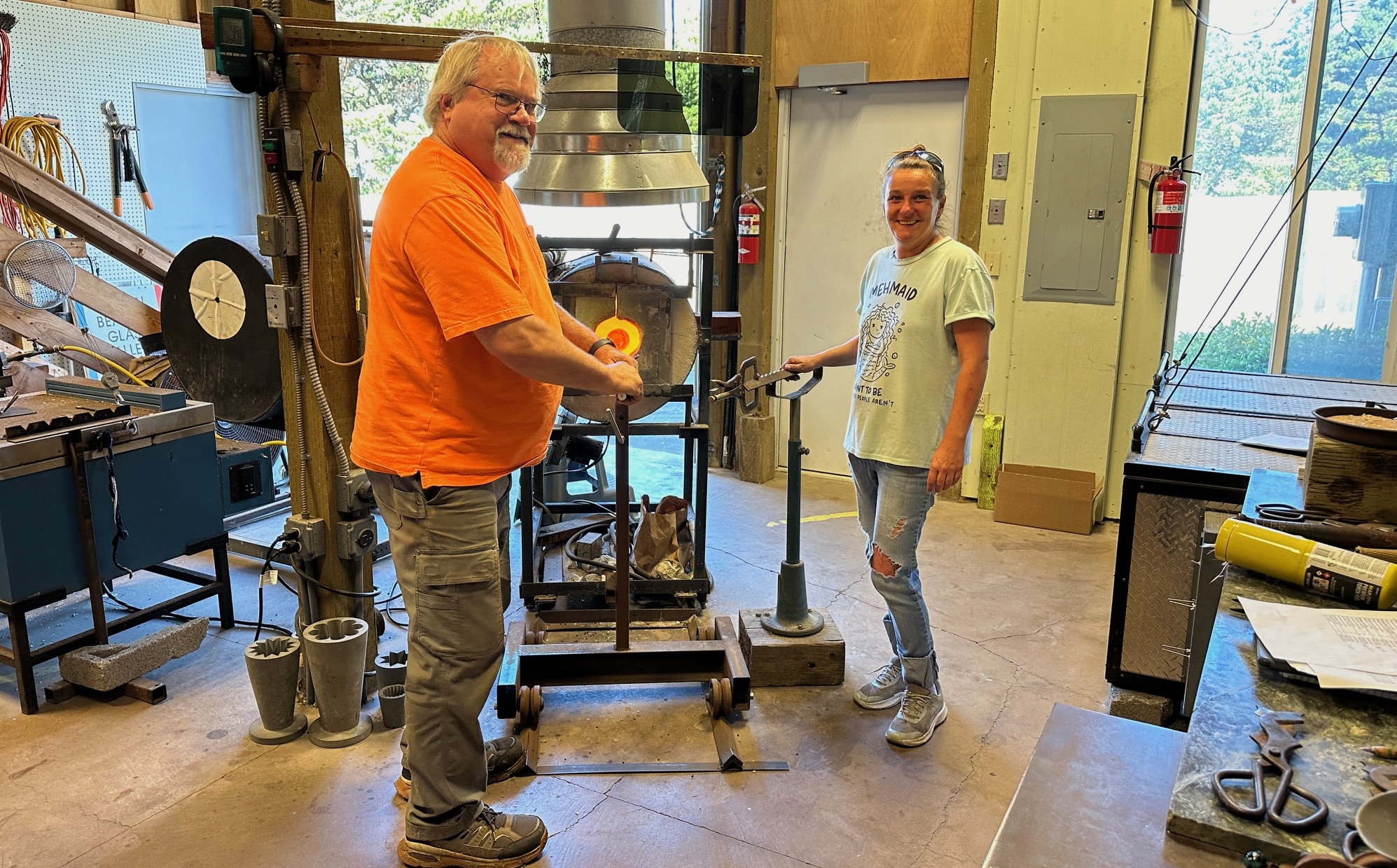
By KATHLEEN O’CONNOR/YachatsNews
SEAL ROCK — Bubbling up, then bursting forth. That’s the way Bob Meyer, owner of Ocean Beaches Glassblowing and Gallery in Seal Rock, describes the creativity was bottled up inside him when he was introduced to glass blowing in 2003.
Meyer had been a pharmacist for many years, a field which is totally structured. He is still a bit astounded by the way his life turned toward imagination and art.
Meyer and his wife, Vicki, moved to Newport in 2001. Bob Meyer had been hired as the pharmacy director at Samaritan Pacific Communities Hospital and Vicki hired as the nurse manager of the surgery department. Both had spent their whole lives in Wisconsin but were looking for a change.
They left the humidity and mosquitoes and snow of Milwaukee behind and as soon as they started their new jobs began exploring the Oregon coast. Meyer was fascinated by a visit to a glass blowing shop.
It didn’t take long for him to decide to learn more, and he took lessons at Pyromania Glass in South Beach for a year. When the year was over he met with Larry Sommer, a glass fuser in Toledo, and together they got Sommer’s mothballed glass blowing equipment up and running.
Meyer started blowing glass every spare minute, and before long he and Vicki decided to set up a shop. They purchased a narrow, deep lot in Seal Rock in 2005 so they could build both a shop and home in the same place. In 2007 Meyer left his job at the hospital and began blowing glass full-time.
Question: How would you explain the dramatic shift you made from being a pharmacist to being a glass blower?
Answer: I really don’t know why I was immediately drawn to glass blowing. In watching the process, I could see that the possibilities for color and shape were endless, and an unexpected passion was awakened in me.
Q: Would you please explain the process of blowing glass?
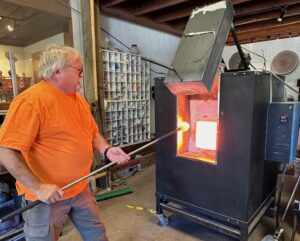
A: There are three pieces of equipment. First, the furnace, which is always kept at 2050 degrees. It is heavily insulated and can keep its heat for about three days even if our electricity goes down. Second, the glory hole, which is heated up each day to 2400 degrees, and shut down at the end of the day. And third, the annealer, which is heated to 920 degrees, and is used to cool the glass.
Glass comes to us from one of only three factories in the form of cullet, which is glass that is manufactured specifically for glass blowing. There are factories in Germany, the Czech Republic and Mexico. We first heat the cullet in the furnace on the end of a pipe until it’s about the consistency of molasses. Then we start to shape it by rolling the pipe on a flat surface. Next we reheat and reshape the glass many times using the glory hole, adding color as we go along. When the piece is done we put it in the annealer to cool. We can’t cool it at room temperature because it would break. It must cool slowly.
Q: How are your pieces different than other glass blowers along the coast?
A: Many glass blowers make structured pieces — bowls that are perfectly round, for example. I always make my pieces without regard for structure. I want each of them to be unique, and the glass and colors seem to work together to make that happen each time. Adding color to glass is very tricky; normal logic about color doesn’t apply. There is no way to know to how added colors will look when a project is finished except through experience.
The most popular pieces in our shop are the glass floats, but I specialize in lampshades. Our lampshades are in three local businesses (the Drift Inn in Yachats, Ocean Bleu at Gino’s in Newport, and the Sea Hag in Depoe Bay), and in many local homes.
We also create memorial glass pieces, encasing a loved one’s ashes within a glass float. Friends and family watch me create this piece. It can be a very intimate, loving experience.
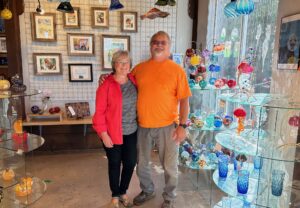
Q: What has Vicki’s role been in the business?
A: Vicki has provided support in every way. We needed someone to provide a regular income at first, and insurance coverage. But more importantly, she could see how passionate I was about glass blowing and provided unconditional assistance and encouragement as we built the business. Now she manages the employees and creates all the displays in the shop.
Q: What does your business look like now, after almost 19 years?
A: Our biggest recent change is that we have another glass blower, Amanda Williams. She is very experienced and has initiated our “experiences” program. In a very nurturing, patient manner she guides people through the process of making a glass object.
Our gallery includes pieces by about 60 other artists, most of them from the central Oregon coast. Not just glass artists, but also painters, photographers and jewelry makers.
Tell me a secret.
I believe that everyone has a creative skill set buried inside them. Many people never discover theirs, and many people don’t discover theirs later in life, often after retirement. I am very grateful to have found mine.
- Kathleen O’Connor is a Waldport freelance writer who can be reached via email at kmoc8916@gmail.com